What to Know About Warehouse Loading Docks
It’s no secret that the last several months have turned warehousing and warehouse design on its head. With eCommerce shopping growing increasingly popular, warehouse loading docks have garnered more attention recently. If you are taking a closer look at what you currently have to upgrade it, it’s important to focus on some factors that need to be implemented in your warehouse loading dock — including elements like usage, safety, maintenance, and more.
What Does Your Dock Do — Really?
How did you initially design your loading dock? The right design means you’ll keep employees safe while also moving inventory in and out quickly and efficiently. Starting from ground-up construction is easy, but you can also apply design best practices to loading docks that can’t be completely renovated. Ask yourself a few questions before nailing down a design:
- How many trucks will be using the docks in 24 hours?
- What are the sizes and frequency of the loads going on and off the trucks?
- Will you be unloading full truckloads or smaller pallets?
- Has there been a recent change in the size and width of trailers pulling up to the docks?
After finding these answers, create a design that includes standard warehouse measurements: a drive approach should equal 150 feet with door centerlines averaging about 12-14 feet. Dock height should be 46-48 inches and minimum overhead door space should be 9 feet wide by 10 feet high.
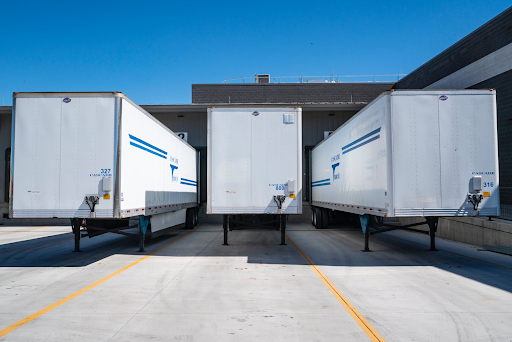
Choose a Dock Style
Your industry and inventory will largely dictate what style of warehouse loading dock you should think about designing. Although it’s not a comprehensive list of utilized layouts, these are three common warehouse loading dock designs to consider:
- Flush loading: This is a pretty standard design where the dock’s foundation is flush with the outside wall of your building and provides a level approach for trucks and trailers.
- Enclosed docks: While this offers a climate-controlled environment and product protection for loading and unloading, it can carry higher construction costs.
- Open loading: This may not be the best design choice if you’re concerned about theft or exposure to the elements. These docks also need a canopy added for protection.
Choose the Right Equipment
Not all warehouse dock equipment is created equal, and the cheapest option is not always the best option. Restraints, master control panels, and barrier gates are sharing the spotlight when choosing the right equipment. While these add-ons can raise the overall investment cost of dock design, they also offer more significant long-term savings and, more importantly, help mitigate safety risks. Restraints that are integrated with master control panels automate the security of the trailer locking into the dock and eliminate manual errors that chocks can present.
Barrier gates can provide an extra layer of safety on docks that are often tight spaces with fall risks. Gates can be fixed into position or offer opening and closing functions that optimize the space and mobility of workers on the dock. Additionally, lighting that alerts when a dock is ready to enter for loading or unloading can be far more effective than a simple yellow line painted on the floor.
Don’t Overlook Warehouse Loading Dock Maintenance
Even the best and most expensive warehouse equipment will eventually suffer wear and tear — which can be mitigated with a comprehensive maintenance plan. With a warehouse loading dock in disrepair, trailers can separate and cause accidents, forklifts and workers can collide, and other loading dock issues can lead to product and facility damage and injuries. The last thing you need is a bad reputation or worse — a lawsuit.
Air or hydraulic levelers may present some with sticker shock, but they require less maintenance and have lower maintenance costs than their mechanical counterparts. Safety regulations may require food and beverage facilities to have tight seals on docks that keep products inside the warehouse protected from moisture, contaminants, and even pests.
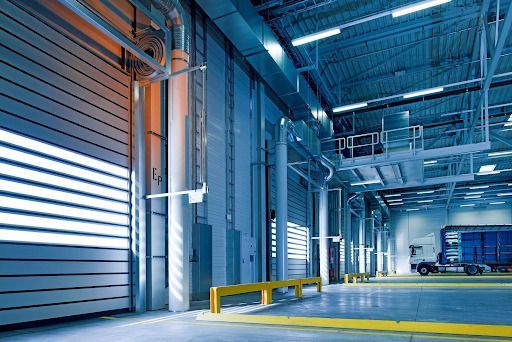
Air Quality Matters!
Proper ventilation may seem like a minor detail, but it goes a long way to keeping your dock employees comfortable during extreme weather. This means you’re not constantly opening doors in the summertime — something that could allow thieves to get a great idea of which valuable assets you may be storing, so keep security in mind too.
Ready to build or upgrade a loading dock design that truly works for your warehouse? Get in touch with our experts who can design, procure, and install the right loading docks and doors for you. Proper warehouse equipment not only makes your operation more efficient, but also makes your business a safer place to work.
The post What to Know About Warehouse Loading Docks appeared first on Benco Industrial Equipment.