Warehouse Dock Design Best Practices
Warehouse Dock Design. Believe it or not, holiday shopping (and shipping!) season is right around the corner. You may have your inventory management down pat and a good handle on your materials handling, but if your loading dock isn’t optimized your whole supply chain could suffer.
Whether you’re building a new warehouse or taking a closer look at what you currently have it’s important to focus on some factors that could make or break your design — including elements like usage, safety, maintenance, and more.
How you use your warehouse dock is key
Be honest: When was the last time you had a close look at how well your dock is designed to promote both safety and efficiency? This is easy if you’re starting from ground-up construction but design best practices can also be applied to loading docks that can’t be completely renovated. Ask yourself a few questions before nailing down a design:
- How many trucks will be using the docks in the course of 24 hours?
- What are the sizes and frequency of the loads going on and off the trucks?
- Will you be unloading full truckloads or smaller pallets?
- Has there been a recent change in the size and width of trailers pulling up to the docks?
Once you’ve determined these answers, create a design that includes a drive approach of 150 feet with door centerlines averaging about 12-14 feet. Dock height should be 46-48 inches and minimum overhead door space should be 9 feet wide by 10 feet high.
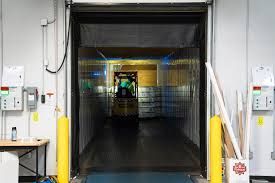
Settle on a warehouse dock style
Depending on your industry, a certain type of loading dock could be better than others. These are three common warehouse loading dock designs to think about, although it’s not a comprehensive list of utilized layouts.
- Flush loading: This is a pretty common design where the foundation of the dock is flush with the outside wall of your building and provides a level approach for trucks and trailers.
- Enclosed docks: While this offers a climate-controlled environment and product protection for loading and unloading, it can carry higher construction costs.
- Open loading: If you’re concerned about theft or exposure to the elements, this may not be the best design choice. These docks also need a canopy added for protection.
Find the right loading dock equipment
Restraints, master control panels and barrier gates are sharing the spotlight when choosing the right equipment. While these add-ons can raise the overall investment cost of dock design, they also offer greater long-term savings and, more importantly, help mitigate safety risks.
Restraints that are integrated with master control panels automate the security of the trailer locking into the dock and eliminate manual errors that chocks can present.
Barrier gates can provide an extra layer of safety on docks that are often tight spaces with fall risks. Gates can be fixed into position or offer opening and closing functions that optimize the space and mobility of workers on the dock. Additionally, lighting to alert when a dock is ready to enter for loading or unloading can be far more effective than a simple yellow line painted on the floor.
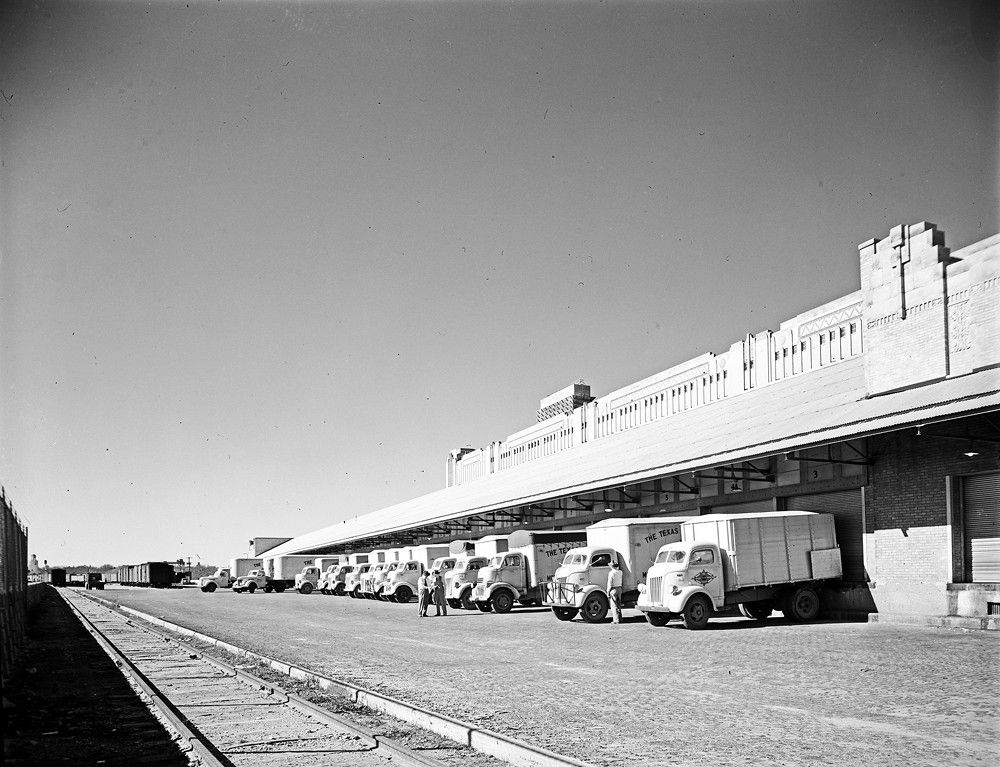
Dock maintenance matters
Along with keeping your dock in top shape, proper maintenance is imperative to support safety. Trailers can separate and cause accidents, forklifts and workers can collide, and other loading dock issues can lead to product and facility damage and injuries. The last thing you need is a bad reputation or worse — a lawsuit.
Air or hydraulic levelers may present some with a bit of sticker shock but they require less maintenance and have lower maintenance costs than their mechanical counterparts. Safety regulations may require food and beverage facilities to have tight seals on docks that keep products inside the warehouse protected from moisture, contaminants, and even rodents.
Keep your warehouse dock secure
Designing your warehouse loading dock to be more secure protects your assets and your employees. Choosing to prevent theft can even help lower your insurance premiums and operating costs. Start by understanding
industry-specific requirements to learn what you need in order to protect your facilities from unwanted intruders. Build on-premise security tech into your design so you can have eyes on your docks 24/7 without having someone on-site.
Proper ventilation may seem like a minor detail, but it goes a long way to keeping your dock employees comfortable during extreme weather. This means you’re not constantly opening doors in the summertime — something that could allow thieves to get a great idea of which valuable assets you may be storing.
Ready to build or upgrade a loading dock design that truly works for your warehouse? Get in touch with our experts who can design, procure, and install the right docks and doors for you. Remember: Proper warehouse equipment not only makes your operation more efficient, it makes your business a safer place to work.
The post Warehouse Dock Design Best Practices appeared first on Benco Industrial Equipment.