How to Maintain Warehouse Facilities
Workplace safety plays a significant role in successful warehouse management strategies, but what are you doing to protect your physical warehouse facility from unnecessary wear, tear, and damage?
When your warehouse building and equipment don’t function as they should, the downtime can directly impact your bottom line. Consider these strategies to help avoid costly repairs to the property or replacing equipment.
Don’t Skip Regular Maintenance
The best way to avoid the cost and downtime that comes with emergency maintenance is to work hard to prevent serious problems from arising in the first place. Routine inspection and equipment maintenance can alert managers and employees to issues that could slow down productivity and cause a safety hazard. A forklift leaking a bit of oil may not seem like a problem until it causes a slip-and-fall accident in your warehouse.
Don’t hesitate to replace outdated or poorly functioning warehouse equipment during this time. Equipment repairs are less costly than replacements, but there may be a time when buying new is the only rational option. Work closely with your vendor to ensure that you’re getting top-quality equipment and a team that can help keep it well-maintained.
Using a warehouse monitoring system can streamline regular maintenance. Whether using warehouse management software or in-person observation, keeping an eye on the floor can help identify potential cleanliness or maintenance issues before they become problematic. Consider offering incentives to employees to help support monitoring initiatives and commit to a safety culture.
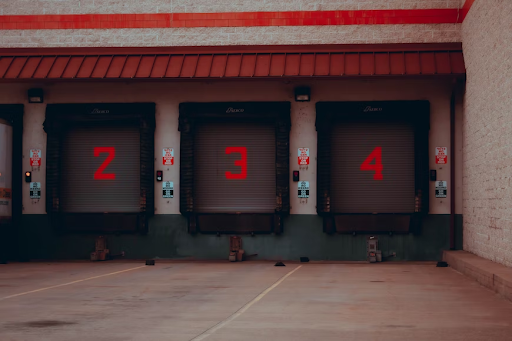
Focus On the Loading Docks
With a warehouse loading dock in disrepair, trailers can separate and cause accidents, forklifts and workers can collide, and other loading dock issues can lead to product and facility damage and injuries. The loading docks are notorious for being a high-traffic hazard.
Air or hydraulic levelers may present some with sticker shock, but they require less maintenance and have lower maintenance costs than their mechanical counterparts. Safety regulations may require food and beverage facilities to have tight seals on docks that protect products inside the warehouse from moisture, contaminants, and even pests.
Barrier gates can provide an extra layer of safety on docks that are often tight spaces with fall risks. Gates can be fixed into position or offer opening and closing functions that optimize the space and mobility of workers on the dock. Additionally, lighting that alerts when a dock is ready to enter for loading or unloading can be far more effective than a simple yellow line painted on the floor. These proactive steps will minimize the damage done to your loading docks.
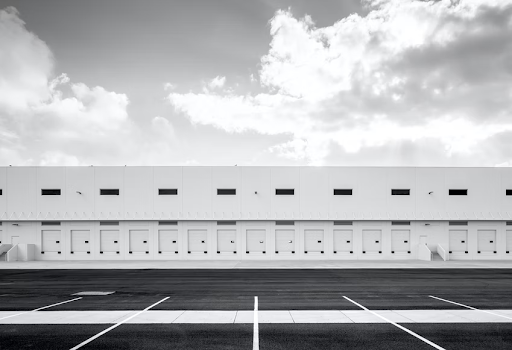
Create an Emergency Plan
Even with a robust seasonal warehouse maintenance plan, it’s crucial to account for emergencies. Toxic spills, fires, hurricanes, and even earthquakes can wreak havoc on your team, and it’s important to prepare everyone for a potential crisis. Maintenance after disaster strikes may look a bit different than what you do on a regular, preventative basis.
This plan should be highly personalized for a variety of situations. Think about the most likely risks to your warehouse and create custom plans. Getting your warehouse back to order after something like a fire requires a different approach than losing power. This is not something that should be one-size-fits-all.
Once you know which resources you’ll need for your plan, make it a team effort. Recruit a handful of key players in your warehouse to be a specialized response team to execute the plan. Keep in mind that they’ll need the experience and certification to perform maintenance on specialized equipment like forklifts or conveyor belts.
Let Us Help
Suppose you’re not sure where to start when maintaining your physical warehouse property and equipment. In that case, it’s wise to consult with warehouse professionals to answer any questions as you move through your seasonal warehouse maintenance.
Turn to us at Benco: We provide sales, installation, service, and repair for the critical equipment in most warehouses. Our technicians are OSHA trained and Factory Certified in Hyundai and PowerBoss equipment. Whether you’re looking for equipment for your newly purchased warehouse or you’re looking to replace aging warehouse supplies, Benco Industrial Equipment can help – contact us today to get started!
The post How to Maintain Warehouse Facilities appeared first on Benco Industrial Equipment.