The Crucial Role of Training in Warehouse Equipment Operation
Operating a warehouse involves more than just storing and moving goods. It is a complex environment with heavy machinery, specialized equipment, and dynamic workflows. Given this complexity, proper training in the use of warehouse equipment is not just beneficial—it is essential.
In this blog post, we'll explore why training is crucial for warehouse workers and its positive impacts on safety, efficiency, and overall operations.
Safety First: Preventing Accidents and Injuries
Safety is the primary reason for thorough training. Warehouses are bustling environments with forklifts, pallet jacks, conveyor belts, and other heavy machinery constantly in use. Without proper training, workers are at a higher risk of accidents, which can range from minor injuries to severe, life-threatening incidents.
Training ensures that employees understand how to operate equipment correctly and safely. They learn to recognize potential hazards, such as overloaded forklifts, improperly stacked pallets, or malfunctioning equipment. By adhering to safety protocols, trained workers can prevent accidents that could cause injuries or even fatalities. Moreover, a safety-first approach helps comply with occupational safety regulations, such as those set forth by OSHA (Occupational Safety and Health Administration), avoiding legal repercussions for the business.
Efficiency and Productivity: Maximizing Output
Beyond safety, training significantly boosts efficiency and productivity. Skilled workers who know how to use warehouse equipment properly can perform tasks more quickly and accurately. For example, a well-trained forklift operator can maneuver the vehicle efficiently in tight spaces, reducing the time to move goods. Similarly, employees trained to use inventory management software can ensure accurate stock level tracking, leading to better inventory control and less downtime.
Training reduces the likelihood of equipment misuse, leading to breakdowns and costly repairs. When employees are knowledgeable about proper maintenance routines and handling procedures, equipment stays in better working condition, further enhancing productivity.
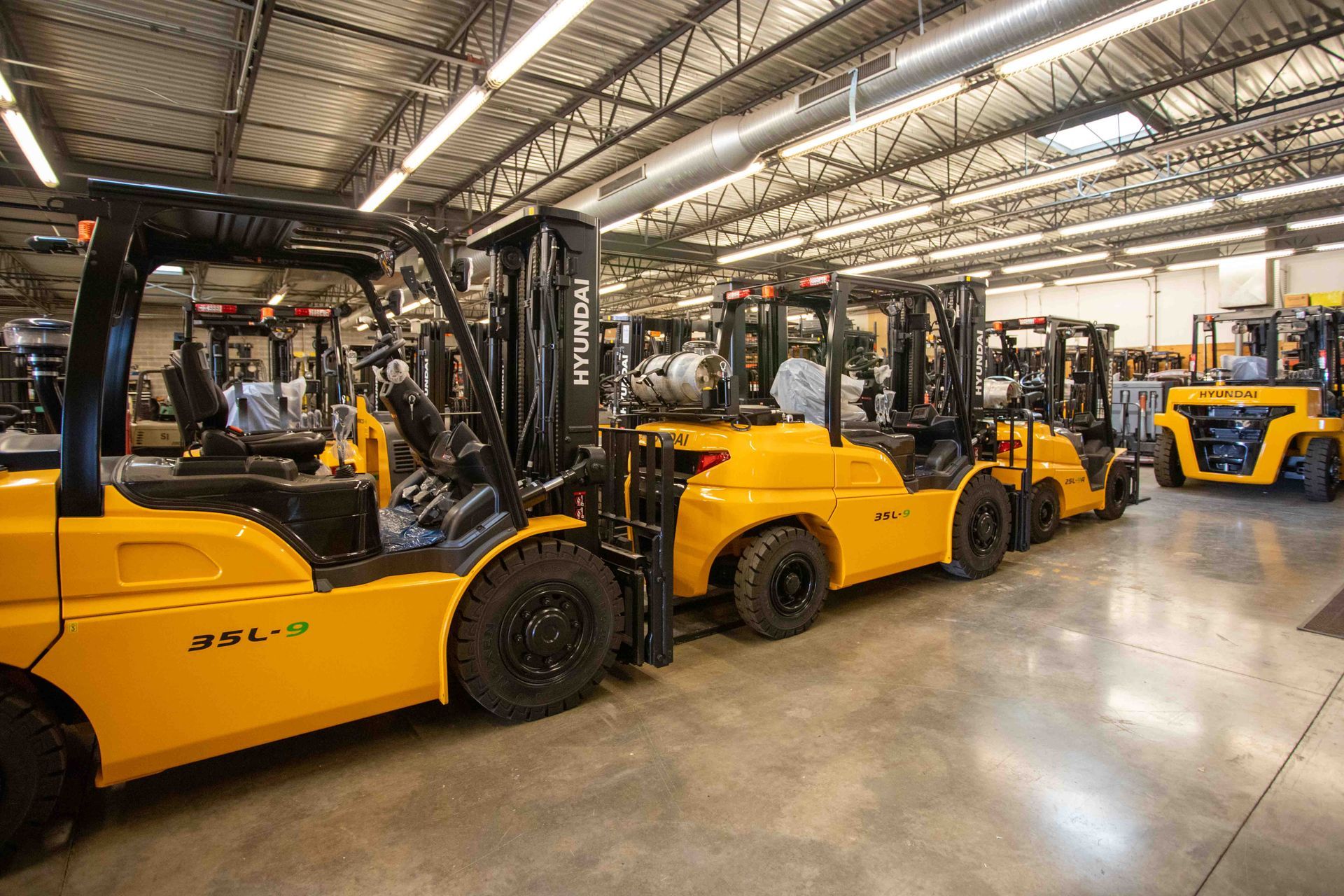
Cost Management: Reducing Expenses
Proper equipment use training also has significant financial benefits. Accidents and equipment damage can be costly. Medical expenses, worker compensation claims, legal fees, and repair costs can quickly increase. By minimizing these risks through practical training, businesses can save substantial money.
Additionally, trained employees are more adept at identifying minor issues before they become significant problems. Routine maintenance and early intervention can extend the lifespan of equipment, reducing the need for expensive replacements and ensuring that machinery operates at peak efficiency.
Employee Morale and Retention: Building a Competent Workforce
Investing in training programs also boosts employee morale and retention. Workers who feel confident and competent in their roles are more likely to be satisfied with their jobs. They appreciate their employer's investment in their professional development, which can lead to increased loyalty and reduced turnover rates.
A well-trained workforce fosters a culture of safety and responsibility. When employees understand the importance of proper equipment use and safety protocols, they are more likely to take ownership of their roles and work collaboratively to maintain a safe and efficient workplace.
Regulatory Compliance: Meeting Legal Requirements
Many industries have strict regulations governing the operation of warehouse equipment. Compliance with these regulations is not optional; it is a legal requirement. Training programs ensure employees know and adhere to these regulations, helping businesses avoid fines and legal issues.
For instance, OSHA mandates that forklift operators complete a certification process that includes formal instruction and practical training. Non-compliance with such regulations can result in hefty fines and, more importantly, endanger workers' lives.
Future-Proofing : Adapting to Technological Advances
The warehouse industry continually evolves, introducing new technologies and equipment regularly. Continuous training helps employees stay up-to-date with the latest advancements and best practices. This adaptability is crucial for maintaining competitiveness in a rapidly changing market.
For example, automation and robotics integration in warehouses is becoming more common. Employees trained to work with these advanced systems can help the business transition smoothly, maximizing the benefits of new technology while minimizing disruptions.
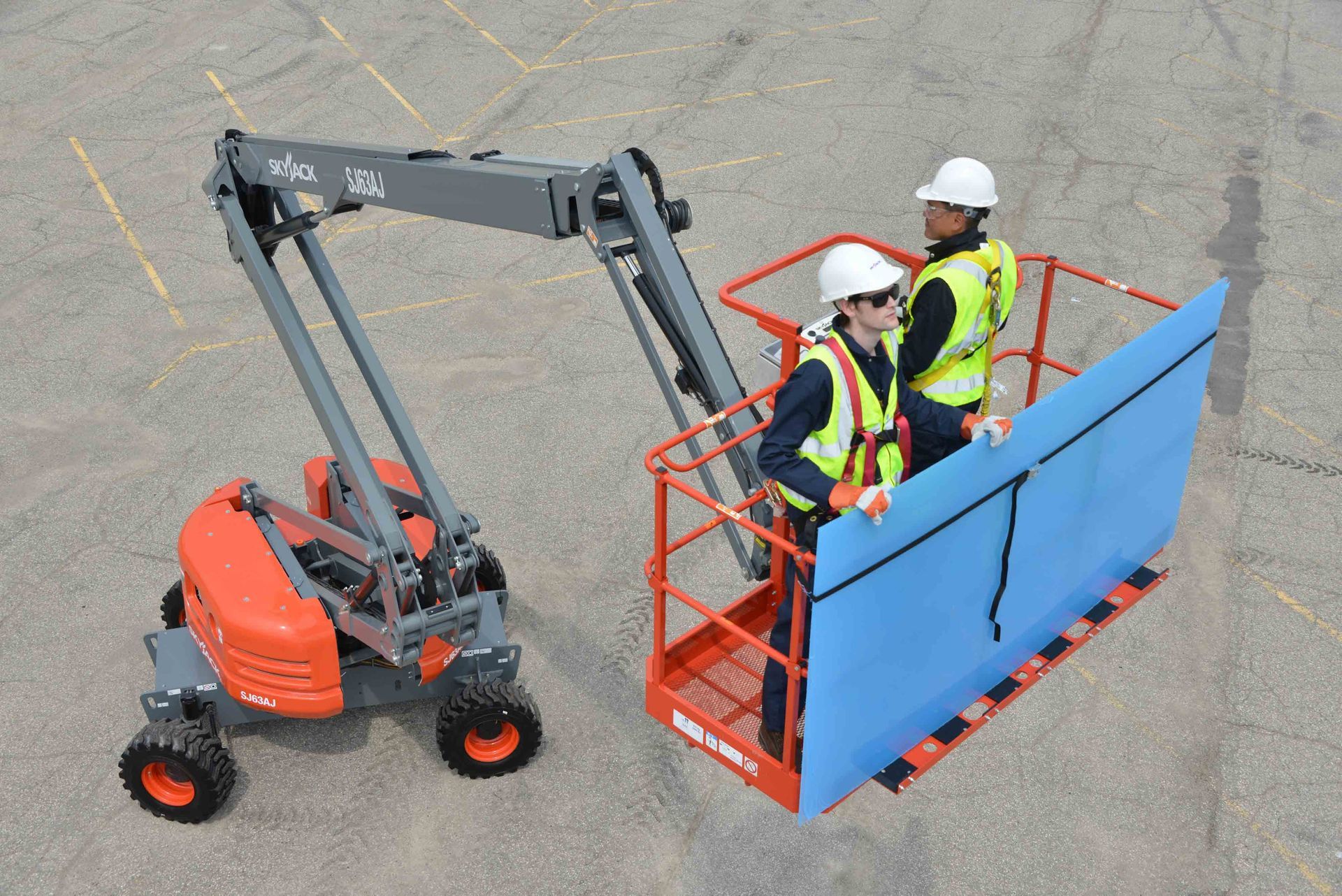
Work With Benco Industrial Equipment
Training warehouse employees to properly use equipment is not merely a procedural formality but a fundamental aspect of effective warehouse management. It enhances safety, boosts efficiency, reduces costs, improves employee morale, ensures regulatory compliance, and prepares the workforce for technological advancements. By investing in comprehensive training programs, businesses can create a safer, productive, and resilient warehouse environment.
Our Benco Industrial Equipment team offers personalized assistance and consultation to help you find the best solutions for your warehouse needs.
Contact us today to explore our range of industrial equipment and services and take the first step toward improving your warehouse operations.