A Guide to Warehouse Signage
Warehouses are fast-paced, inherently dangerous worksites, which means there needs to be clear, accurate signage that protects pedestrians and equipment operators alike. Strategic warehouse signage can also keep the facility well-organized and boost the productivity of employees.
Although those are just a few reasons to utilize warehouse signage, you should really invest in warehouse signage to stay compliant with the Occupational Safety and Health Administration (OSHA) and the American National Standards Institute (ANSI).
Warehouse Signage Types
The type of signage you choose for your warehouse depends on the location it’s in and the purpose it’s used for.
Safety: This is probably the most important warehouse signage category, used to inform visitors and employees of safety requirements and best practices.
Exit/Egress: When an emergency or a power outage happens in your warehouse, there needs to be clear and accurate signage that lets everyone know where to safely exit the building.
Aisles/Rows: Aisle and row identifiers should be large, bright, and well-located so employees can easily and quickly locate inventory and optimize the picking process.
Dock Doors: Drivers and workers need to know where to go to drop off or pick up inventory, and loading docks need clear signage to indicate where to do that.
Hanging: These signs hang from the ceiling of warehouses and have reflective barcodes that can be identified with long-range scanners to locate bulk items.
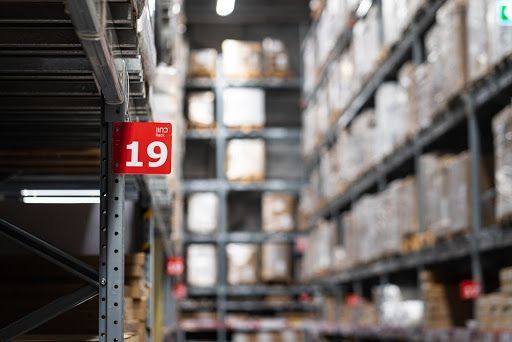
Benefits of Warehouse Signage
It makes warehouses safer: Even beyond the explicit signage designed for safety, increased awareness throughout the space helps employees move more safely and confidently throughout their workday.
It increases productivity: When employees know where to go and how to easily access inventory, their workflows are streamlined and their productivity is boosted. This is especially true for warehouses that rotate inventory on a seasonal basis.
It improves warehouse efficiency: Clear signage can mitigate the risk of order fulfillment errors, increasing customer satisfaction and streamlining operations. Signage can also keep inventory well organized and orderly.
Think About OSHA
You’ll need to consult OSHA guidelines when choosing signage for your warehouse, but generally, it’s divided into different categories: Caution signs warn employees about potential safety hazards, safety instruction signs offer important guidance, and danger signs indicate immediate danger where precautions are necessary.
In addition to colors, lettering, size, OSHA has some other requirements for warehouse signage:
- Sign Headers: OSHA prescribes sign headers to have a trigger word in block or capitalized letters that contrast with the background. Black is the universal color for header words.
- Sign Format: OSHA recommends that workplace safety signs have a specific format. That includes the trigger word or sign information category at the top, an ANSI-approved hazard symbol at the mid and lower left.
- Sign Font: Using the right font on warehouse safety signs is essential. OSHA recommends using a sans-serif font like Ariel, Verdana, or Helvetica which is easy to read, especially from a distance. Just as contrasting colors are essential, so is having a non-cluttered font that’s well-recognized.
- Sign Materials: OSHA recommends all workplace signs to have durable material that mounts well and withstands all environmental conditions. They recommend having rounded corners without sharp edges.
- Sign Visibility: As a rule, the common-sense approach is to increase the font size to correspond with the intended readable distance. For example, at 5 feet, the text size should be a quarter-inch tall. At 40 feet, it should be 1.6 inches high, and at 100 feet, the font needs to be at least 4 inches.
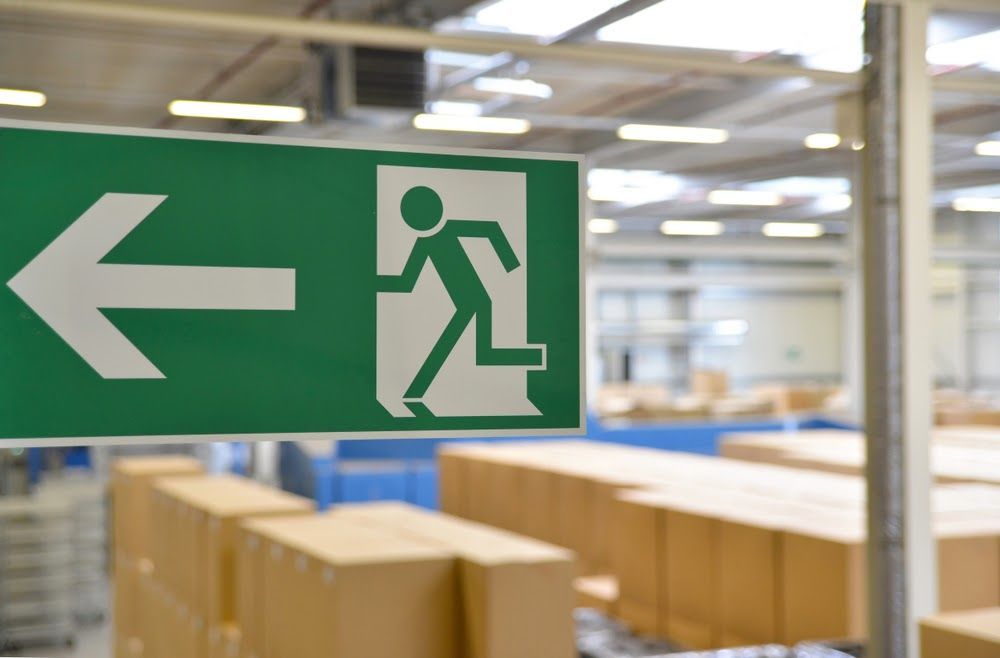
When it comes to keeping your warehouse safe, signage goes a long way — but so does maintaining your warehouse equipment. Benco Industrial Equipment has proudly served the material handling needs of customers in the St. Louis Metro Area and throughout the Midwest for over 15 years.
Whether you’re looking for equipment for your newly purchased warehouse or you’re looking to replace aging warehouse supplies, Benco Industrial Equipment can help. We are the best source for forklift service, repair, sales, and leasing in St. Louis, St. Charles, Jefferson County, and the surrounding areas!
We also provide MacroAir fans, warehouse doors and docks, warehouse racks and racking, floor sweepers, and much more! We respond in minutes, not days, to assure our customers always have the material handling equipment they need to keep their warehouses running smoothly. Our staff is experienced in handling all sorts of industrial equipment issues, from forklift repair to installing new warehouse doors, so no matter your need, our team of industrial equipment experts can help.
The post A Guide to Warehouse Signage appeared first on Benco Industrial Equipment.